خواص پوشش الکترولس - نیکل فسفر - نیکل سخت
خواص پوشش الکترو لس نیکل با پوششی که از طریق جریان الکتریکی تولید شده بسیار متفاوت است که دلیل آن مکانیزم ایجاد پوشش و وجود فسفر و یا بور در پوشش می باشد .
مقاومت به خوردگی خوب ، سختی زیاد ، ضریب اصطکاک کم ، مقاومت به سایش مناسب ، غیر مغناطیس بودن ، قابلیت لحیم کاری و یکنواخت بودن پوشش های الکترولس نیکل باعث شده است که کاربرد وسیعی در رشته های مهندسی داشته باشد.
ظاهر و درخشندگی :
بر خلاف پوشش های نیکل حاصل از از روش جریان الکتریکی که دارای رنگ زرد ملایمی هستند ، پوشش الکترولس نیکل شبیه به فولاد براق اند و رنگی تقریبا نقره ای دارند . به دلیل مقاومت مطلوبی که در مقابل تیره شدن دارند ، نسبت به پوشش های الکتریکی به مدت طولانی تری براق باقی می مانند . انواع پوشش های الکترولس نیکل تقریبا همرنگ هستند .
چسبندگی :
چسبندگی پوشش های الکترولس نیکل بر روی بیشتر فلزات فوق العاده خوب است . واکنش هایی که در طول پوشش دادن بین محلول الکترولس نیکل و فلز پایه رخ می دهد باعث می شود که باند های فلزی یا مکانیکی با فلز پایه به وجود آید . با انجام عملیات حرارتی چسبندگی پوشش افزایش می یابد که به دلیل ایجاد باند های شیمیایی بین فلز پایه و پوشش می باشد . گرمایش و سرمایش را باید به آهستگی انجام داد تا از به وجود آمدن ترک های ریز جلوگیری شود . چسبندگی پوشش به کیفیت تمیز کردن سطح و عملیات قبل از پوشش دادن بستگی دارد .
چگالی پوشش :
چگالی فلز نیکل در دمای اتاق 8.9 گرم بر ساتی متر مکعب است و چگالی پوشش نیکل که از روش الکتریکی ایجاد شده با استفاده از حمام وات بین 8.89 تا 8.391 است . در حالی که چگالی پوشش الکترولس نیکل به میزان فسفر پوشش بستگی دارد و با افزایش میزان فسفر پوشش چگالی پوشش کاهش می یابد ، شکل زیر یکی از روش های اندازه گیری چگالی پوشش با استفاده از فرمول زیر است :
فرمول 1-1 روش اندازه گیری چگالی پوشش |
𝝆= چگالی پوشش
Wt=وزن فلز پایه +پوشش ( در هوا )
Ws=وزن فلز پایه ( در هوا )
Wtl= وزن فلز پایه +پوشش ( در مایع)
Wsl=وزن فلز پایه ( در مایع )
Liq 𝝆= چگالی مایع
نمودار تاثیر میزان فسفر بر روی چگالی پوشش
تخلخل :
در پوشش هایی که نسبت به فلز پایه نجیب ترند تخلخل بسیار مهم است و تاثیر زیادی روی مقاومت به خوردگی پوشش و فلز پایه دارد . خواص دیگری همچون چگالی ، قابلیت لحیم کاری و چکش خواری وابستگی زیادی به میزان تخلخل پوشش دارند . ذرات روی ، کادمیم و آلمینیوم فعال تر از آهن و قلع ، مس و نقره ، نیکل و کبالت نجیب تر از آهن اند.. در پوشش های الکترولس نیکل ضخامت های کمتر از 25 میکرو متر معمولا متخلخلند و مقاومتشان در برابر خوردگی کم است . با افزایش ضخامت میزان تخلخل ها هم کم می شودو مقاومت به خوردگی افزایش می یابد .
نقطه ی ذوب :
نقطه ی ذوب پوشش الکترولس نیکل – فسفر به درصد فسفر بستگی دارد . با افزایش میزان فسفر پوشش ، دمای ذوب کاهش می یابد . در حالی که دمای ذوب نیکل خا لص 1450 درجهی سانتیگراد است . پوشش الکترولس نیکل- فسفر با مقدار 7 تا 9 درصد فسفر دارای دمای ذوب 800 درجه سانتیگراد می باشد .
خواص حرارتی و الکتریکی :
خواص حرارتی و الکتریکی پوشش الکترولس نیکل با تغییر ترکیب حمام عوض می شود و در ترکیبات مختلف خواص متفاوتی به دست می آید . برای پوشش های تجارتی مقاومت الکتریکی و هدایت حرارتی به ترتیب برابر با 50 تا 90 میکرو اهم بر سانتیمتر و 0.01 تا 0.013 کالری بر سانتیمتر ثا نیه می باشد . این پوشش ها معمولا هدایت الکتریکی کمتری نسبت به مس و نقره دارند .با انجام عملیات حرارتی بر روی پوشش ، هدایت الکتریکی 3 تا 4 برابر خواهد شد . مقدار فسفر همچنین اثر زیادی روی انبساط حرارتی الکترولس دارد . پوشش با نیکل بیش از 10% فسفر کاملا غیر مغناطیس و پوشش با فسفر کمتر از 10% کمی مغناطیسی است . عملیات حرارتی در دمای بیش از 200 درجه ی سانتیگراد باعث افزایش خاصیت مغناطیسی پوشش الکترولس نیکل می شود . شکل زیر نشان میدهد که ضریب انبساط حرارتی پوشش با فسفر زیاد تقربا با فولاد برابر است :
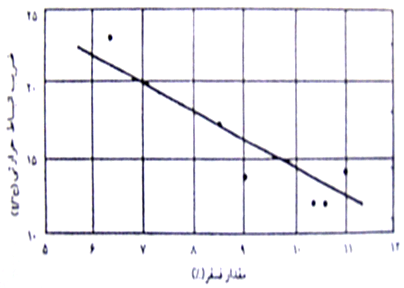
نمودار تاثیر میزان فسفر بر روی انبساط حرارتی
تنش های داخلی :
تنش داخلی در پوشش های الکترولس نیکل به ترکیب پوشش وابسته است . در پوشش های الکترولس نیکل نیکل با فسفر بیشتر از 10.5 % تنش به صورت فشاری و در کمتر از آن تنش کششی است . شکل زیر اثر میزان فسفر را روی تنش داخلی نشان می دهد . شرایط پوشش و عمر حمام تاثیر مهمی روی تنش پوشش خواهد داشت و با افزایش عمر حمام میزان تنش هم زیاد خواهد شد . شکل زیر تاثیر فسفر بر روی تنش های داخلی را نشان میدهد :
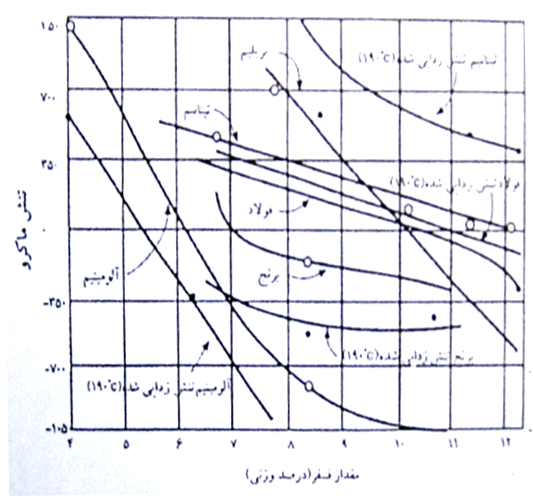
نمودار تاثیر میزان فسفر بر روی تنش داخلی
انعطاف پذیری :
انعطاف پذیری یکی از خواص مهم مکانیکی پوشش الکترولس نیکل است . انعطاف پذیری به میزان فسفر پوشش بستگی دارد . با افزایش فسفر به حدود 5% انعطاف پذیری کاهش می یابد و تا 9% نیز ثابت می ماند و سپس با افزایش میزان فسفر ، انعطاف پذیری بیشتر می شود . شکل زیر اثر میزان فسفر را روی انعطاف پذیری نشان می دهد:
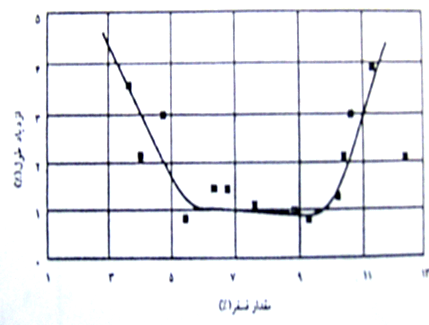
نمودار تاثیر میزان فسفر بر روی انعطاف پذیری
قابلیت لحیم کاری :
پوشش های الکترولس نیکل خاصیت لحیم کاری مطلوبی دارند و اگر از روانساز مناسب استفاده شود ، کار آسانتر خواهد شد . پیشگرم کردن هم باعث افزایش سهولت و سرعت کار می شود .
استحکام کششی :
استحکام کششی پوشش الکترولس نیکل به مقدار فسفر پوشش بستگی زیادی داد . برای پوششی با مقدار فسفر کم استحکام کششی بین 45 تا 50 کیلیوگرم بر میلی متر مربع می باشد . بعد از عملیات حرارتی در دمای 300 تا 600 درجه سانتی گراد استحکام کششی کاهش خواهد یافت . شکل زیر اثر میزان فسفر را روی استحکام کششی نشان می دهد :
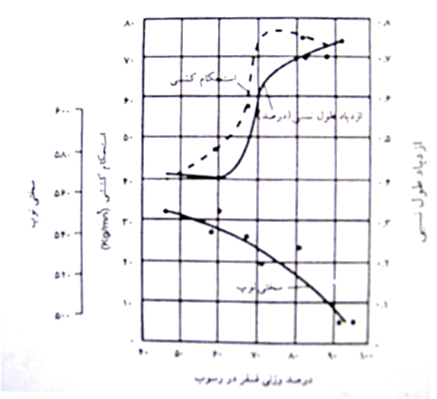
شکل 1-13 نمودار تاثیر میزان فسفر بر روی استحکام کششی پوشش
سختی و مقاومت سایشی :
سختی و مقاومت سایشی مهمترین ویژگی های پوشش الکترولس نیکل اند که باعث کاربرد وسیع این پوشش شده اند. میکرو سختی پوشش تقریبا برابر 500 الی 600 است که تقریبا برابر با 48 تا 52 راکول سی است و با سختی فولاد الیاژی برابر است . عملیات حرارتی باعث افزایش سختی تا حدود 1100 می شود که با پوشش کروم سخت برابر است .
تاثیر عملیات حرارتی بر روی سختی پوشش در شکل زیر آمده است :
شکل 1-14 نمودار تاثیر عملیات حرارتی بر روی سختی پوشش
بهترین سختی در دمای 400 در جه سانتیگراد و در مدت 1 ساعت به دست آمده است . بعضی اوقات که به علت احتمال تاب خوردن قطعه نمی توان از دما های زیاد استفاده کرد ، از دما های کم و زمان های طولانی برای عملیات حرارتی استفاده می شود . عملیات حرارتی به علت ایجاد ذرات سرامیکی بسیار سخت Ni-P در ساختار ، سختی پوشش را افزایش می دهد . با افزایش میزان فسفر سختی پوشش هم کاهش می یابد .
با توجه به سختی زیاد پوشش الکترولس نیکل میزان سایش هم کم است . این ویژگی موجب کاربرد وسیع پوشش های الکترولس نیکل در مواردی شده است که مقاومت سایشی زیاد مورد نیاز است .
با انجام عملیات حرارتی میزان مقاومت به سایش هم افزایش می یابد و لی بیشترین مقاومت سایشی در دمای 600 درجه سانتیگراد حاصل می شود . یعنی بیشترین مقاومت سایشی در بیشترین سختی به دست نیامده است . مقاومت سایشی فلزات بستگی به سختی ، چقرمگی شکست و میکرو ساختار دارد . بنابر این چون میزان سایش علاوه بر سختی به انعطاف پذیری هم بستگی دارد و بهینه ی سختی و انعطاف پذیری در دمای 600 درجه ی سانتیگراد ظاهر می شود ، بنابر این کمترین سایش در دمای 600 درجه ی سانتیگراد دیده می شود . طبق شکل زیر :
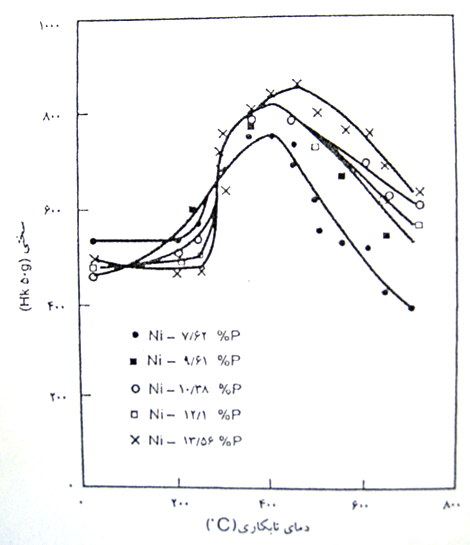
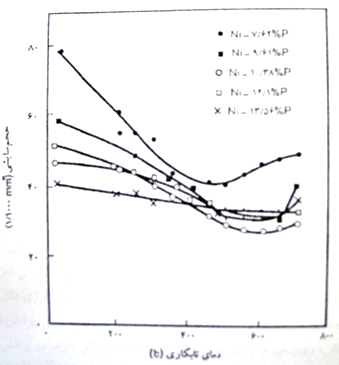
استحکام خستگی :
از آنجا که پوشش الکترولس نیکل تحت بار های سیکلی دچار ترک می شود ، موجب ککاهش استحکام خستگی فلز پایه می شود . میزان کاهش استحکام خستگی به ترکیب محلول ، نوع عملیات حرارتی و ضخامت پوشش بستگی دارد. پوشش الکترولس نیکل معمولا باعث کاهش 10 تا 50 درصدی از استحکام خستگی و حد تحمل فاز پایه می شود. در پوشش هایی که بیشتر از 10% فسفر دارند مشکلی دیده نمی شود و در برابر ایجاد ترک مقاوم اند .
مقاومت به خوردگی :
پوشش الکترولس نیکل پوشش محافظی است که با جدا کردن فلز پایه از محیط ، آن را محافظت می کند . بنابر این رسوب باید عاری از هر گونه تخلخل باشد . به دلیل ساختار بی شکل مقاومت به خوردگی بسیار عالی است و در بسیاری از محیط ها از نیکل خالص بهتر است. معمولا ساختار بی شکل ، نسبت به مواد پلی کریستال مقاومت بهتری دارند که دلیل آن وجود مرزدانه ها در مواد پلی کریستال است. مقاومت به خوردگی در محیط خنثی و اسیدی با افزایش مقدار فسفر پوشش افزایش می یابد و عکس این مطلب در محیط های قلیایی صادق است . مقاومت به خوردگی فلز پایه و پوشش تابع موارد زیر است :
_ نوع پوشش الکترو لس نیکل
_ نوع ساختار فلز پایه
_ ضخامت پوشش
_ شرایط پوشش
_ عملیات آماده سازی
_ روش انجام آزمایش
عملیات حرارتی تاثیر مهمی روی مقاومت خوردگی پوشش دارد . هنگامی که پوشش حرارت می بیند از دمای 220 درجه ی سانتیگراد به بعد فسفر تبدیل به فسفید نیکل می شود که در نتیجه مقدار فسفر پوشش کاهش می یابد و این باعث کاهش مقاومت به خوردگی پوشش می شود . این ذرات همچنین پیل های کوچک ، اکتیو – پسیو ایجاد می کنند که موجب خرابی بیشتر پوشش می شود .